The Art and Science of Plastic Injection Mold Making
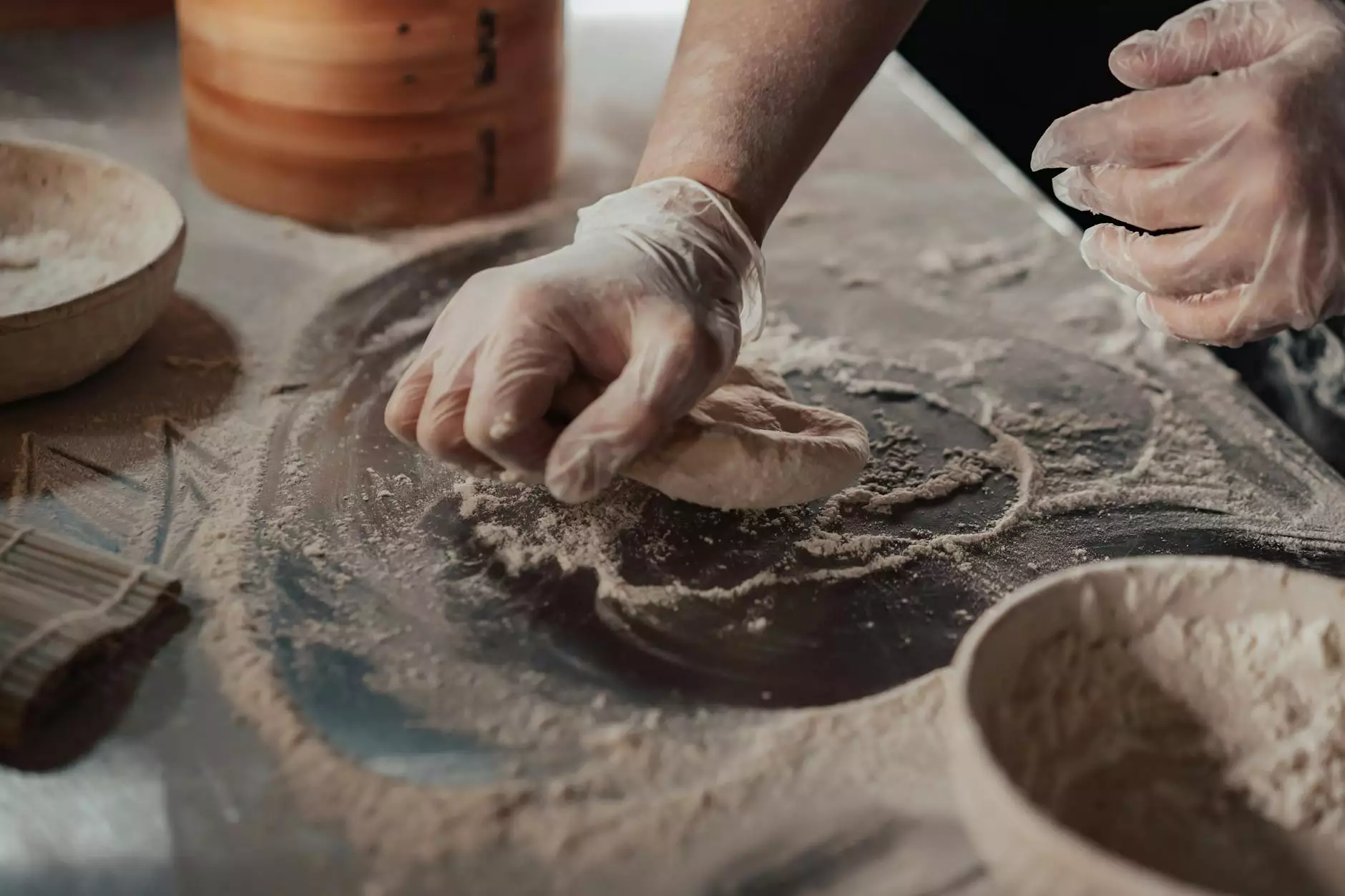
Plastic injection mold making stands as a cornerstone in the realm of manufacturing, playing an essential role in the production of a vast array of plastic components. This intricate process not only champions the efficiency of mass production but also maintains an unparalleled standard of quality and precision. In this article, we delve deep into the key aspects of plastic injection mold making, exploring its benefits, techniques, applications, and much more to provide a comprehensive understanding of this vital industry.
Understanding Plastic Injection Molding
At its core, plastic injection molding is a manufacturing process that involves injecting molten plastic material into a mold cavity. This method enables the creation of intricate shapes and designs with remarkable accuracy. The process begins with plastic pellets, which are melted and injected into a finely crafted mold. Once the plastic cools and solidifies, the mold is opened to reveal the finished part. This allows for the mass production of identical components with high precision and minimal waste.
The Process of Plastic Injection Mold Making
The process of plastic injection mold making involves several key steps, each critical to ensuring the final product's quality and functionality:
- Designing the Mold: The process begins with designing the mold using advanced CAD (Computer-Aided Design) software. This design phase is crucial, as it determines the shape and functionality of the final product.
- Material Selection: Choosing the right materials for both the mold and the plastic is essential. The mold is typically crafted from metals such as steel or aluminum, chosen for their durability and heat resistance.
- Mold Fabrication: Once the design and materials are finalized, the mold is fabricated. This step often employs CNC (Computer Numerical Control) machining, ensuring precise manufacturing of the mold components.
- Injection Process: With the mold ready, the injection process begins. Molten plastic is injected into the mold cavity under high pressure, filling all intricacies and ensuring a perfect imprint of the mold's design.
- Cooling and Ejection: After the plastic injection, the material needs time to cool and solidify. Once cooled, the mold opens to eject the finished plastic part.
Benefits of Plastic Injection Mold Making
Plastic injection mold making offers a plethora of benefits that make it a preferred choice for manufacturers across various industries. Here are some of the prominent advantages:
- High Efficiency: Injection molding allows for the rapid production of large volumes of parts, making it highly efficient for mass manufacturing.
- Cost-Effectiveness: Although the initial costs for mold creation can be high, the per-unit cost decreases significantly with larger production runs.
- Precision and Quality: The precision of the mold design ensures that each produced part is identical, meeting high-quality standards.
- Design Flexibility: The process supports complex designs, enabling manufacturers to create intricate shapes that would be impossible using other methods.
- Material Variety: A wide range of plastic materials can be used, including thermoplastics, thermosets, and composites, allowing for versatile product applications.
Applications of Plastic Injection Mold Making
The applications of plastic injection mold making are vast and encompass numerous industries. Some notable sectors include:
Aerospace and Automotive
In the aerospace and automotive industries, components produced via injection molding are essential for structural integrity, safety, and functionality. Parts such as connectors, brackets, and housings are commonly manufactured through this method.
Consumer Electronics
The consumer electronics sector relies heavily on plastic injection molding for producing casings, bezels, and other components that require intricate design and precise fitting.
Medical Devices
In the medical field, where precision and sterility are paramount, plastic injection mold making enables the manufacturing of various devices, including syringes, surgical instruments, and housings for electronic equipment.
Packaging
Plastic injection moulds are also utilized in the packaging industry, producing containers, caps, and other packaging solutions that require lightweight and durable plastic materials.
Challenges in Plastic Injection Mold Making
While the advantages are significant, plastic injection mold making comes with its own set of challenges that manufacturers must navigate:
- High Initial Costs: The initial investment in designing and fabricating molds can be substantial, which may deter smaller companies.
- Complex Process: The need for skilled professionals to design, manufacture, and operate molding machines adds complexity and increases costs.
- Maintenance Challenges: Molds require regular maintenance and occasional repairs to ensure consistent quality and functionality.
- Environmental Concerns: The industry faces scrutiny regarding the environmental impact of plastic production and disposal.
The Future of Plastic Injection Mold Making
As industries evolve, so does the technology and methods used in plastic injection mold making. Several trends are shaping the future of this vital industry:
Innovation in Materials
The introduction of bioplastics and other sustainable materials is gaining momentum as manufacturers seek greener alternatives for plastic production. This trend reflects the industry's commitment to environmental responsibility.
Advancements in Technology
Technological innovations, such as 3D printing, are increasingly being integrated into the mold-making process, leading to faster prototyping and more cost-effective designs. Additionally, automation in injection molding machinery is improving operational efficiency and precision.
The Rise of Smart Manufacturing
With the advent of Industry 4.0, smart manufacturing processes are becoming mainstream. Utilizing IoT (Internet of Things) for monitoring and maintenance can reduce downtime and improve the overall productivity of plastic injection molding.
Conclusion
In conclusion, plastic injection mold making is an art form and a science that is crucial to modern manufacturing. Its ability to produce high-quality, cost-effective plastic parts in large volumes is unmatched. As technology continues to advance and industries adapt, the future of plastic injection molding holds great promise, contributing to innovations that will propel manufacturing into new frontiers.
About Deepmould.net
Deepmould.net stands at the forefront of the metal fabricators sector, specializing in providing high-quality solutions tailored to meet the diverse needs of its clients. With a focus on innovation and precision, Deepmould.net integrates cutting-edge technology and expert craftsmanship in every project, ensuring optimal outcomes in plastic injection mold making and beyond.
plastic injection mold maker