The Revolution of Silicone Rubber Injection Molding Machines in Industry
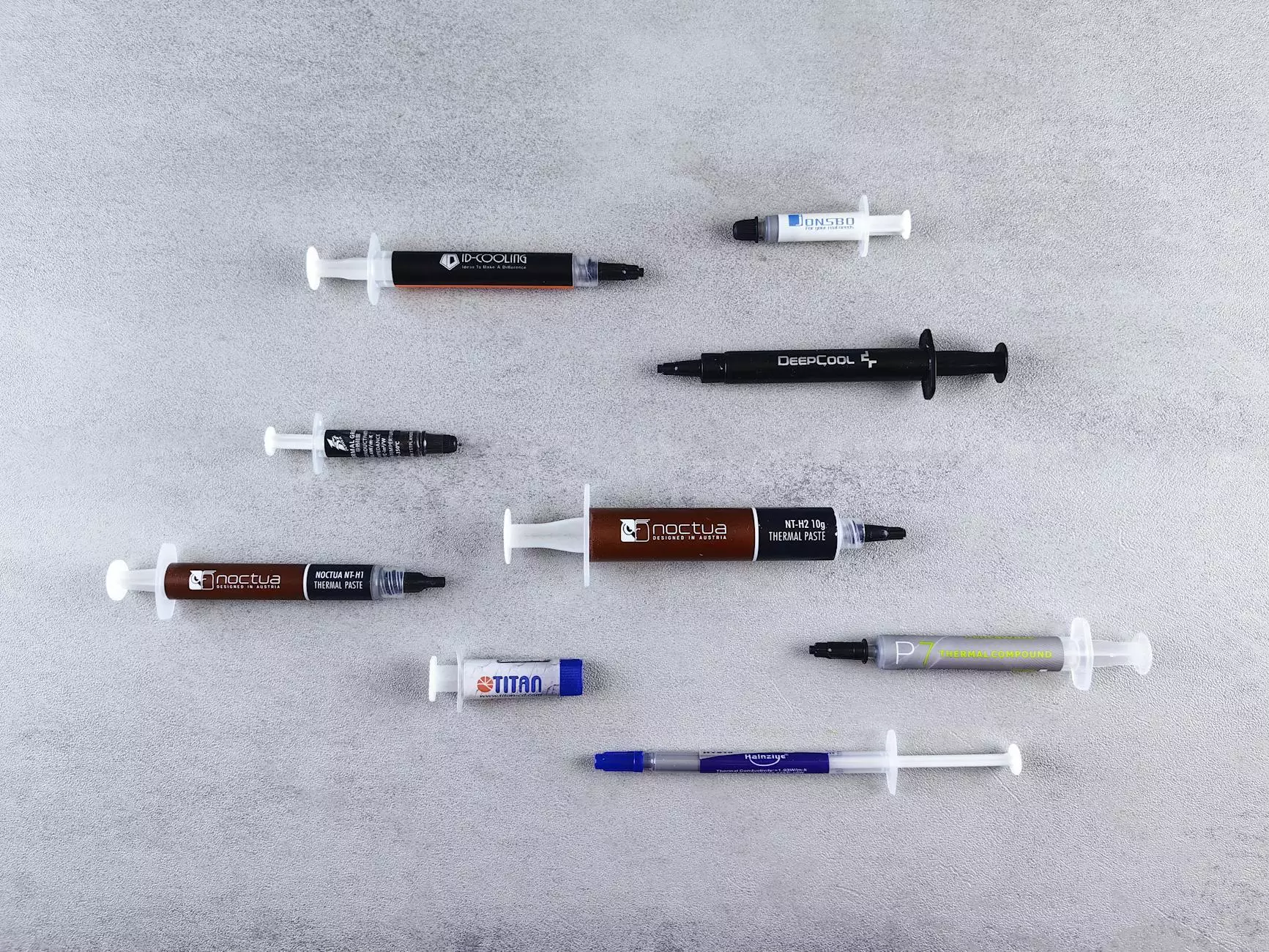
In the modern manufacturing landscape, the term silicone rubber injection molding machine is becoming increasingly prominent. As industries evolve, the demand for high-quality materials and efficient production methods is paramount. This article dives deep into the incredible benefits of silicone rubber injection molding, its technologies, and its applications, particularly in the Electronics and Medical Supplies sectors, where companies like Nolato are setting new standards.
What is Silicone Rubber Injection Molding?
Silicone rubber injection molding is a sophisticated industrial process that transforms silicone polymer into intricate shapes and designs through the use of an injection molding machine. This method involves melting silicone materials and injecting them into molds under high pressure, enabling the production of detailed and complex parts with remarkable precision.
Key Advantages of Silicone Rubber Injection Molding
1. Versatility in Design
The silicone rubber injection molding machine offers unmatched versatility in product design. Manufacturers can create a wide array of products ranging from small components to large assemblies, making it indispensable in various industries.
2. Superior Material Properties
Silicone materials exhibit excellent thermal stability, flexibility, and resistance to extremes of temperature, which makes them ideal for a multitude of applications. This ensures that the final products are durable and reliable, especially in critical environments such as healthcare.
3. Consistent Quality Production
With the precision engineering behind silicone rubber injection molding machines, manufacturers can expect consistent quality in their products. This reduces waste and ensures that each piece meets the stringent requirements of high-tech industries like electronics and medical supplies.
4. Cost Efficiency
While the initial investment in a silicone rubber injection molding machine can be significant, the long-term savings on materials, labor, and energy can make it a cost-effective solution. Production runs can be optimized, and the efficiency of mass production can lead to lower costs per unit.
Applications of Silicone Rubber Injection Molding Machines
Silicone rubber injection molding machines have found applications in various sectors, particularly in Electronics and Medical Supplies. Here’s an overview of how these industries benefit from this innovative technology.
Electronics
The electronics industry demands materials that can withstand high temperatures and harsh environments. Silicone rubber is renowned for its electrical insulation properties, making it a favored choice for components like seals, gaskets, and connectors.
- Seals and Gaskets: Silicone rubber provides excellent compressive strength and flexibility, ideal for protecting sensitive electronic components from environmental factors.
- Insulating Materials: Silicone's dielectric properties ensure reliable performance in insulating applications, particularly in high-voltage environments.
- Keypads and Covers: The soft and flexible nature of silicone allows for the creation of tactile keypads, an essential feature in many consumer electronics.
Medical Supplies
In the medical field, where safety and sterility are paramount, silicone rubber injection molding machines are used to produce numerous medical devices and components.
- Medical Tubing: Silicone's biocompatibility makes it ideal for use in IV and other medical tubing applications, providing flexibility and durability without compromising safety.
- Implants: Silicone rubber is often employed in the manufacturing of implants due to its conformity to the body and resistance to degradation, ensuring long-term efficacy.
- Diagnostics: Devices such as syringes, dental molds, and lab equipment benefit from the precise manufacturing capabilities of silicone rubber injection molding.
The Technology Behind Silicone Rubber Injection Molding Machines
The evolution of silicone rubber injection molding technology has facilitated advanced manufacturing capabilities. Here’s a look at what goes into these machines.
Machine Components
A typical silicone rubber injection molding machine comprises several components that work in harmony:
- Injection Unit: Responsible for melting and injecting silicone into molds, ensuring a consistent flow.
- Mold Closing Mechanism: Ensures that the mold is tightly closed during injection to prevent defects.
- Cooling System: Regulates the temperature of the mold to cool the silicone quickly, enhancing cycle times.
- Control System: Allows for precision control over temperature, pressure, and injection speed, ensuring high-quality production.
Process Steps
The process of silicone rubber injection molding can be broken down into several key steps:
- Material Preparation: Silicone rubber is prepared and loaded into the injection unit.
- Heating and Melting: The silicone is heated until it reaches a molten state, ready for injection.
- Injection: The molten silicone is injected into the mold at high pressure.
- Curing: The silicone is allowed to cure, solidifying into the desired shape.
- Cooling: The mold is cooled to facilitate the removal of the final product without damage.
- Demolding: The finished part is removed from the mold, ready for further processing or assembly.
The Future of Silicone Rubber Injection Molding
As industries continue to evolve, the role of silicone rubber injection molding machines will become increasingly crucial. With advancements in technology, manufacturers are exploring smart manufacturing techniques, integrating IoT (Internet of Things) capabilities, and the use of 3D printing technologies to enhance design flexibility and production efficiency.
Sustainability Focus
Moreover, sustainability is becoming a key driving force in manufacturing. Companies are looking for ways to reduce waste and utilize eco-friendly materials. The flexibility of silicone provides opportunities for innovation in this area, particularly in developing recyclable or bio-based silicone materials.
Conclusion
In summary, the silicone rubber injection molding machine represents a vital evolution in the manufacturing landscape, particularly for industries reliant on precision and quality such as Electronics and Medical Supplies. As technology advances and the need for sustainable practices grows, this method of production will likely see even greater adaptation and innovation.
Companies like Nolato are at the forefront of these changes, driving improvements in product quality, efficiency, and sustainability through state-of-the-art manufacturing processes. For organizations looking to invest in reliable and high-performance solutions, silicone rubber injection molding presents an exceptional opportunity to enhance their product offerings and streamline operations.
Understanding the nuances of silicone rubber injection molding not only equips manufacturers with the knowledge to excel in today’s competitive market but also positions them for future advancements in technology and sustainability.