High-Quality Tooling Die Casting: The Future of Metal Fabrication
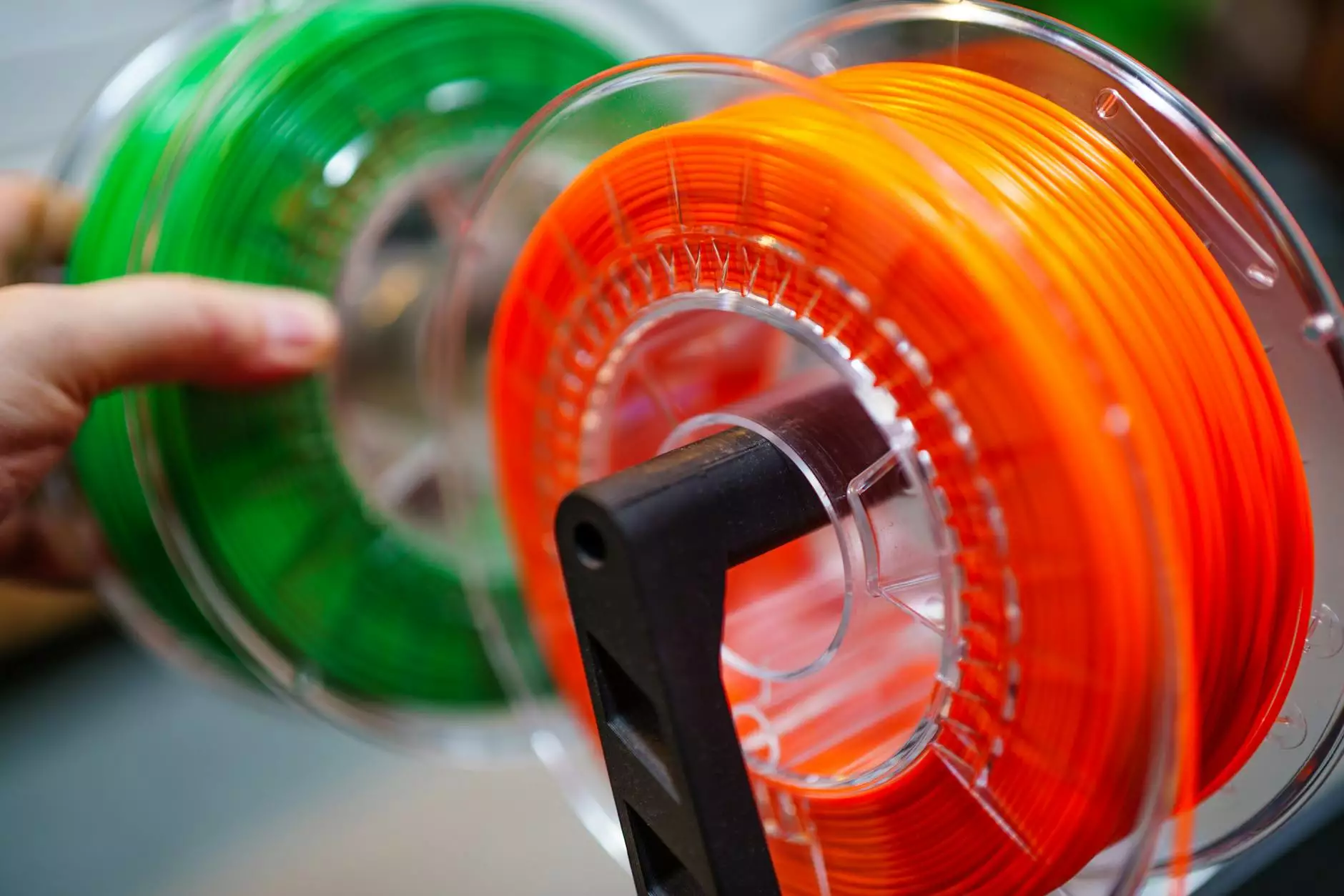
Tooling die casting is not just a manufacturing process; it's a cornerstone of modern metal fabrication that has transformed industries and facilitated the development of a vast array of products. In today's fast-paced world, understanding the fundamentals of this process and its implications on metal fabricators like Deep Mould is essential for businesses aiming to innovate and thrive.
Understanding Tooling Die Casting
At its core, tooling die casting is a manufacturing technique that involves pouring molten metal into a mold to create intricate shapes and designs. This method is favored across various industries for its ability to produce parts with exceptional dimensional accuracy, surface finish, and overall strength.
The Process of Tooling Die Casting
The tooling die casting process can generally be broken down into several key stages:
- Design and Prototyping: This initial phase involves creating a design that outlines the specifications and functionality of the component.
- Mold Creation: Once the design is confirmed, high-quality molds are created, which can withstand the immense heat and pressure during the casting process.
- Melting the Metal: The chosen metal, often aluminum or zinc, is melted in a furnace to reach a molten state.
- Injection into Mold: The molten metal is injected into the mold at high pressure, ensuring that it fills every cavity.
- Cooling and Solidification: After injection, the metal cools and solidifies, taking the shape of the mold.
- Mold Removal: Once solidified, the mold is opened, and the casted part is removed.
- Finishing Process: Any necessary finishing touches are applied, such as trimming excess material or polishing the surface.
This systematic approach not only guarantees high-quality parts but also increases efficiency and reduces production waste.
The Advantages of Tooling Die Casting
The benefits of employing tooling die casting in manufacturing are numerous and impactful:
- High Precision: The process allows manufacturers to produce parts with tolerances as tight as ±0.1mm, ensuring an impeccable fit and function.
- Enhanced Surface Finish: The technique leads to parts with smooth surfaces, reducing the need for extensive post-casting machining.
- Cost-Effectiveness: For high-volume production runs, tooling die casting is often more economical compared to other methods, primarily due to reduced machining and finishing costs.
- Material Efficiency: The process utilizes metals efficiently, minimizing waste and ensuring that even intricate designs are feasible.
- Replication Capability: Tooling die casting is excellent for duplicating parts consistently, making it ideal for mass production.
A Closer Look at Materials Used
The choice of materials in tooling die casting impacts not only the cost but also the performance of the final product. Commonly used metals include:
- Aluminum: Lightweight, corrosion-resistant, and excellent thermal properties make aluminum an industry favorite.
- Zinc: Known for its good strength, ductility, and aesthetic finish, zinc is ideal for small, complex parts.
- Magnesium: Although less common, magnesium alloys offer a superior strength-to-weight ratio.
Applications of Tooling Die Casting
Tooling die casting finds applications across a multitude of sectors:
- Automotive Industry: Used for engine components, transmission housings, and decorative parts.
- Electronics: Employed in creating casings for electronic devices that require durability and precision.
- Aerospace: Critical for lightweight, high-strength components used in aircraft and spacecraft.
- Consumer Goods: Utilized for household appliances, tools, and decorative hardware that benefit from cost-efficient production.
Deep Mould's Commitment to Excellence
Deep Mould is at the forefront of tooling die casting technology, empowering businesses to achieve their manufacturing goals with unparalleled efficiency and quality. With decades of experience, Deep Mould has honed its processes to ensure that every cast meets the highest standards of precision and aesthetic appeal.
Challenges in Tooling Die Casting
No process is without its complications. Some of the challenges faced in tooling die casting include:
- Mold Design Complexity: The intricacy involved in creating molds that can withstand high pressures and temperatures is paramount.
- Defects and Quality Control: Addressing issues such as air pockets, cold shuts, and shrinkage is crucial for maintaining product integrity.
- Material Limitations: Not all metals are suitable for die casting; understanding these limitations is important for optimal production.
The Future of Tooling Die Casting
As industries evolve, so does the need for innovative tooling die casting techniques. New technologies such as 3D printing of molds, improved materials, and automation are revolutionizing the landscape:
- 3D Printing: This technology allows for rapid prototyping and experimentation with complex geometries that were previously difficult to achieve.
- Sustainable Manufacturing: The industry is moving towards eco-friendly practices, utilizing recyclable materials and optimizing energy consumption.
- Smart Manufacturing: Integrating IoT and AI into the die casting process enhances quality control and operational efficiencies, paving the way for future growth.
As a leader in the metal fabrication sector, Deep Mould not only adapts to these changes but also drives them forward, ensuring quality and precision in every component produced.
Conclusion
In conclusion, tooling die casting remains an essential process within the realm of metal fabrication. Its myriad advantages, such as precision, efficiency, and cost-effectiveness, make it a preferred choice for manufacturers across multiple industries. Deep Mould is dedicated to pushing the boundaries of what is possible in die casting, serving as a reliable partner for businesses looking to innovate and stay competitive in a rapidly changing market.
For more information on how tooling die casting can benefit your business or to learn more about Deep Mould's services, visit deepmould.net today!