The Importance of Prototype Mold in Modern Manufacturing
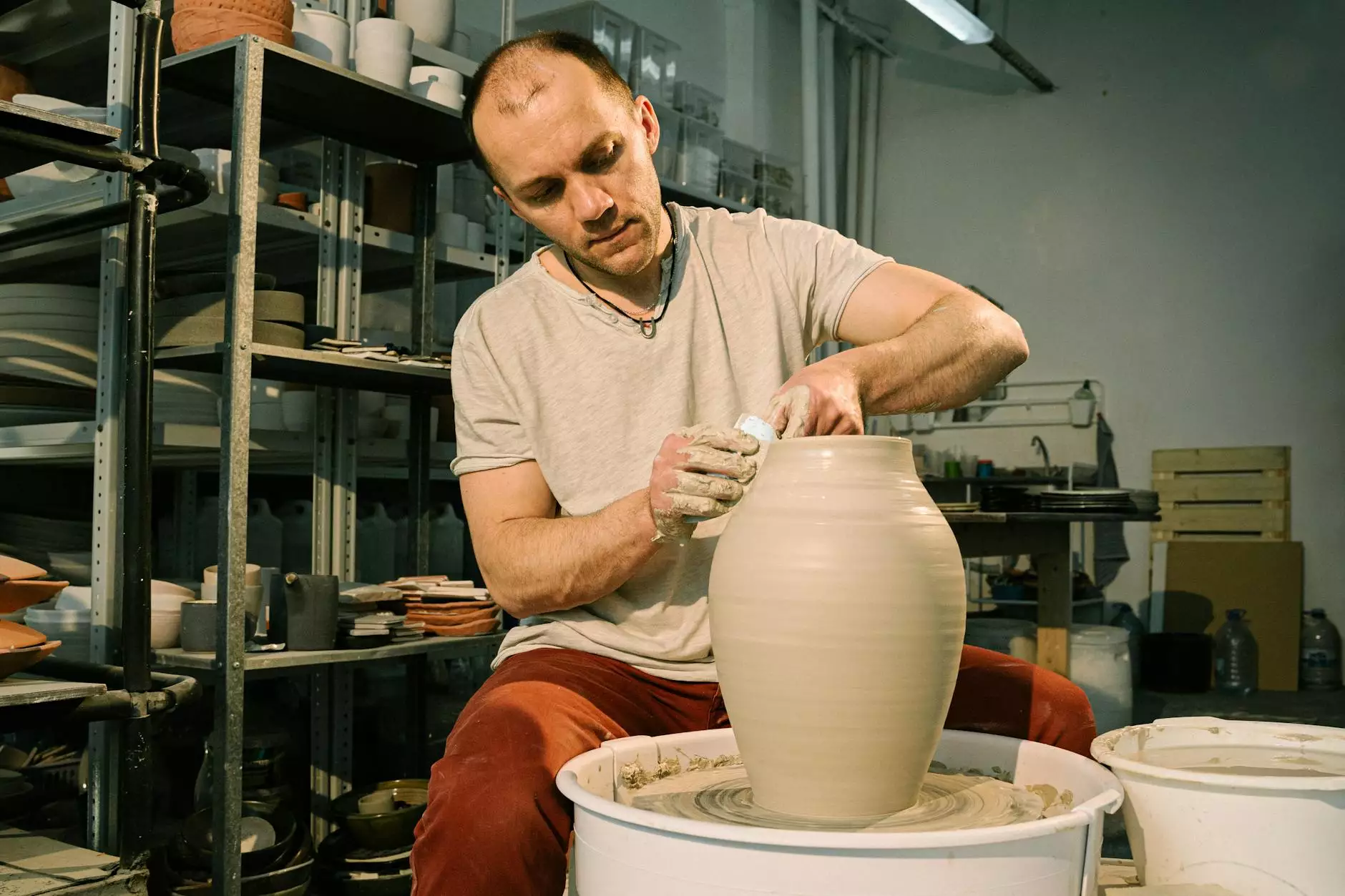
In the rapidly evolving world of manufacturing, the need for high-quality products and precise components has never been greater. One of the crucial elements that ensures superior output in production processes is the utilization of a prototype mold. This article delves deep into the functionality, advantages, and applications of prototype molds, particularly within the realm of metal fabrication. At deepmould.net, we understand the intricate dynamics of producing effective prototypes that lead to successful end products.
What is a Prototype Mold?
A prototype mold is an essential tool used in the early stages of product development. Its primary purpose is to create a preliminary version of a product, allowing manufacturers to evaluate design concepts, test functionalities, and identify any potential issues before final production. Typically made from materials such as steel, aluminum, or other alloys, these molds ensure that the prototype accurately represents the intended final product.
The Process of Creating a Prototype Mold
Understanding the process of creating a prototype mold is vital for anyone involved in manufacturing. Here’s a detailed breakdown of the steps involved:
- Conceptualization and Design: The first step involves brainstorming ideas and generating designs that meet defined product specifications. CAD (Computer-Aided Design) software is often utilized to create detailed drawings and schematics.
- Material Selection: Selecting the appropriate materials for both the prototype and the mold is crucial. Factors such as durability, weight, and thermal properties play a significant role in this decision.
- Mold Fabrication: Skilled metal fabricators create the mold based on the designs. Techniques such as CNC machining, injection molding, and 3D printing may be employed during this phase.
- Prototyping: The mold is then used to produce the prototype. This step involves pouring, injecting, or otherwise applying material into the mold to create the test product.
- Testing and Evaluation: Once produced, the prototype undergoes rigorous testing to identify any design flaws or functional issues and assess its performance against the initial specifications.
- Refinement: Based on the feedback obtained during testing, necessary modifications are made to the mold and design, ensuring the final prototype meets all criteria.
Benefits of Using Prototype Molds
Employing prototype molds offers numerous advantages that directly contribute to successful product development:
- Cost Efficiency: By identifying issues early in the design phase, companies can avoid costly mistakes during mass production.
- Time Savings: Quick iterations and adjustments can be made to prototypes, significantly reducing the time it takes to reach the final product.
- Improved Product Quality: With the ability to test and refine designs, the final product is more likely to meet quality standards and customer expectations.
- Enhanced Communication: Prototypes serve as tangible representations of ideas, facilitating better communication among design teams, stakeholders, and clients.
- Market Validation: Prototypes allow for early market testing and feedback, aiding in understanding customer needs and preferences.
Applications of Prototype Molds in Metal Fabrication
Within the metal fabrication sector, prototype molds serve various applications. Some key areas where these molds are utilized include:
1. Automotive Industry
The automotive sector heavily relies on prototype molds to produce components such as chassis, engine parts, and body panels. Rapid prototyping accelerates the overall design process, ensuring vehicles are not only functional but also aesthetically pleasing.
2. Aerospace Manufacturing
In aerospace manufacturing, precision is paramount. Prototype molds are used for creating intricate components and assemblies that require exact specifications, contributing to enhanced safety and performance.
3. Consumer Electronics
With the rise of smart devices, the consumer electronics industry utilizes prototype molds to develop casings, connectors, and other essential components that must be both lightweight and robust.
4. Medical Devices
The creation of medical devices often requires prototypes to meet strict regulatory standards. Prototype molds help in developing instruments and equipment, allowing for extensive testing before full-scale production.
Why Choose DeepMould.net for Your Prototype Mold Needs?
At DeepMould.net, we pride ourselves on our expertise in creating high-quality prototype molds. Here are some reasons why we stand out:
Expert Team
Our talented team of engineers, designers, and metal fabricators work collaboratively to ensure that your prototypes meet and exceed expectations. Their combined experience leads to innovative solutions tailored for your specific needs.
Advanced Technology
We employ the latest technology in mold making and prototyping, including CNC machining and 3D printing. This ensures precision, accuracy, and efficient production cycles.
Customized Solutions
Every project is unique. At DeepMould.net, we offer customized mold solutions to meet individual project requirements. Our team works closely with you throughout the development process to provide input and support.
Commitment to Quality
We maintain rigorous quality control standards. Each prototype mold undergoes extensive testing to ensure reliability and performance in the final product, aligning with industry regulations and standards.
Competitive Pricing
We understand the financial aspects of project development. Our competitive pricing strategy ensures that you receive high-quality prototype molds without exceeding your budget.
Future Trends in Prototype Mold Development
As technology advances, the development of prototype molds is also evolving. Here are some trends we can expect in the near future:
Increased Use of 3D Printing
3D printing technology is revolutionizing how molds are created. It allows for rapid iterations, more complex designs, and reduced lead times in mold production.
Integration of AI and Machine Learning
Artificial intelligence in mold design can optimize the prototyping process, helping predict potential issues and improving efficiency in design iterations.
Sustainability Practices
With a growing emphasis on sustainability, manufacturers are increasingly looking at eco-friendly materials and processes in the production of prototype molds.
Conclusion
In conclusion, the role of a prototype mold in modern manufacturing cannot be overstated. It serves as a vital tool in product development, aiding companies in achieving desired outcomes effectively while saving time and resources. At DeepMould.net, we are committed to leveraging our expertise in metal fabrication to provide top-notch prototype molds tailored to meet your specific needs. Whether you're in the automotive, aerospace, consumer electronics, or medical device industry, we have the skills and technology to help you succeed.